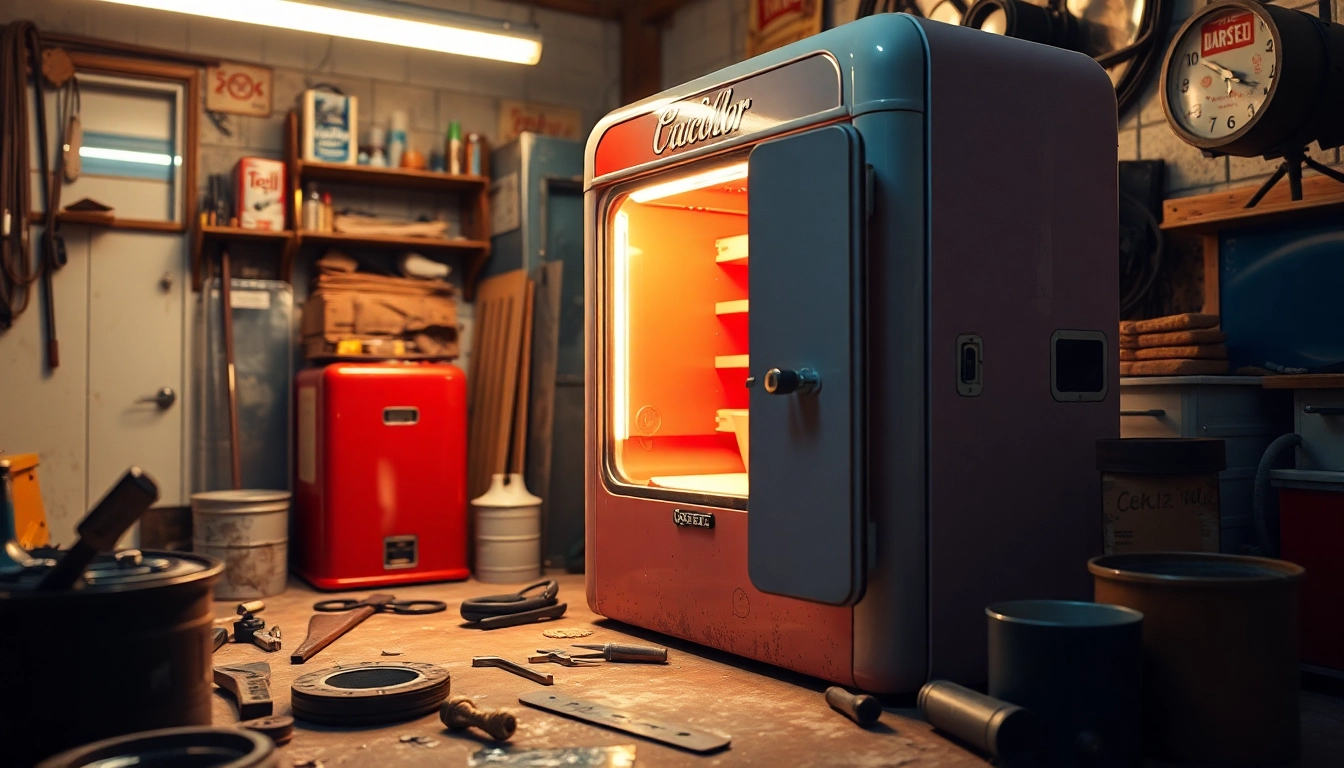
Understanding Common Soda Cooler Issues
Soda coolers are essential appliances for businesses that require chilled beverages to meet customer demand. However, like any machine, they can experience a variety of issues that can disrupt their performance. Understanding these common problems is the first step in effective soda cooler repair. Addressing these symptoms quickly can save both time and money while ensuring that your drinks remain refreshing.
Identifying Cooling Problems
One of the most prevalent issues with soda coolers is inadequate cooling. If you notice that your cooler is not maintaining the desired temperature, it is crucial to start diagnosing the problem. Common reasons for this include:
- Faulty compressor: This is often the heart of cooling systems. A malfunction may prevent the compressor from engaging properly, causing insufficient cooling.
- Dirty condenser coils: Dust and grime can build up on the condenser coils, reducing their ability to dissipate heat. Regular cleaning of these coils is essential for optimal performance.
- Low refrigerant levels: A refrigerant leak can significantly impact the cooling efficiency of your soda cooler.
- Thermostat issues: If the thermostat is malfunctioning, it may not signal the compressor accurately, leading to cooling discrepancies.
Electrical Failures and Solutions
Electrical components within soda coolers can fail, leading to a variety of operational issues. Here are some common electrical failures and their solutions:
- Power supply problems: Ensure that the cooler is properly plugged in and that the outlet is functioning. A simple test can confirm this.
- Faulty relays: The relay is responsible for starting the compressor. If it fails, the cooler won’t operate. Replace any faulty relays.
- Wiring issues: Inspect wires for signs of wear or damage, as frayed wires can disrupt power flow.
Maintenance Tips to Prevent Breakdowns
Preventing breakdowns is often easier and less costly than repairing a soda cooler. Regular maintenance can extend the life of your cooler and improve its efficiency. Consider the following maintenance tips:
- Regular cleaning: Dust and dirt can impair functionality, so clean the condenser coils and external surfaces regularly.
- Inspect seals and gaskets: Check door seals to ensure they are airtight, preventing cold air from escaping.
- Scheduled professional servicing: Having a qualified technician assess your cooler annually can help identify potential issues before they escalate.
Soda Cooler Repair: Tools and Parts You Need
When it comes to soda cooler repair, having the right tools and parts on hand is essential for a smooth and efficient process. Below, we outline the necessary items you may need to effectively address common problems.
Essential Tools for the Repair Process
Equipping yourself with the right tools can make repairs simpler and more efficient. Here are some essential tools:
- Screwdrivers: A variety of Phillips and flat-head screwdrivers can help you dismantle various cooler components.
- Multimeter: A multimeter is invaluable for checking electrical issues and ensuring proper current flow.
- Wrench set: Wrenches are necessary for securing and removing bolts and nuts during repair.
- Vacuum pump: If you need to recharge the refrigerant, a vacuum pump is essential for removing moisture from the cooling system.
Common Replacement Parts for Soda Coolers
During repairs, you may find the need to replace certain components. Here are some of the most common replacement parts:
- Compressors: If your compressor is failing, it’s often necessary to replace it entirely.
- Thermostats: A faulty thermostat can drastically affect temperature control, so replacement may be needed.
- Expansion valves: These valves help regulate refrigerant flow and may need replacement if cooling issues are present.
- Condenser fan motors: These are vital for proper cooling as they help dissipate heat. A malfunctioning fan can cause overheating.
Where to Source Parts for Your Cooler
Obtaining the right parts quickly is vital to ensuring your cooler is back in working order. Here are some good sources to consider:
- Online retailers: Websites like Amazon, eBay, and specialty appliance parts websites can be excellent resources.
- Local appliance parts stores: These stores often stock a variety of commonly needed parts.
- Manufacturer’s website: The official website for your cooler brand may sell direct replacement parts.
Step-by-Step Guide to Soda Cooler Repair
If you decide to tackle the repair on your own, following a step-by-step guide can simplify the process. Here’s how to effectively repair your soda cooler.
Initial Assessment and Diagnosis
Diagnosing the problem accurately is the first step. Begin with a visual inspection:
- Look for any visible signs of wear, such as frayed wires, rust, or leaks.
- Check the power source to ensure the cooler is receiving electricity.
- Test components, using a multimeter as necessary to assess their functionality.
Repairing the Cooling System
Once diagnosed, you can begin the pertinent repairs:
- Replace any faulty parts identified during your assessment, ensuring you follow correct procedural steps.
- If necessary, recharge the refrigerant in the system. Be mindful of environmental regulations regarding refrigerants.
- Clean or replace the condenser coils to maximize efficiency.
Testing and Final Adjustments
After repairs, it’s essential to test the cooler:
- Replug the unit and monitor it for a while to ensure it achieves and maintains the desired temperature.
- Continue to check for any unusual noises or leaks that may indicate issues.
- Make adjustments as necessary to refrigerant levels and thermostat settings.
Cost Considerations for Soda Cooler Repair
Understanding the potential costs associated with soda cooler repairs is crucial for budgeting and decision-making. Below, we explore various cost considerations.
Estimated Costs for Common Repairs
The cost of repairs can vary depending on the issue. Here are some average estimates for common repairs:
- Compressor replacement: This can range from $400 to $800, depending on the model and labor costs.
- Thermostat replacement: Costs generally fall between $100 and $300.
- Refrigerant recharge: Expect to pay around $100 for this service, not including any potential leaks that need fixing.
- Fan motor replacement: This repairs typically cost $150 to $400, depending on the motor type.
Do-It-Yourself vs. Professional Help
One major decision will be whether to undertake repairs yourself or hire a professional. Factors influencing this decision include:
- Skill level: If you have experience with appliances, a DIY approach can save money.
- Time constraints: Professional repairs may be faster, as they can quickly diagnose and fix issues.
- Risk of further damage: Incorrect repairs can worsen the issue; in such cases, hiring a professional may be more cost-effective.
Long-Term Savings Through Preventive Maintenance
Investing in preventive maintenance can significantly reduce repair costs over time. Regularly scheduled check-ups can:
- Identify potential failures before they occur, greatly reducing emergency repair costs.
- Ensure the cooling efficiency of your soda cooler remains high, preserving product quality.
- Extend the lifespan of your equipment, enabling it to operate optimally for longer.
When to Seek Professional Help for Soda Cooler Repair
While many repairs can be done independently, some situations warrant professional assistance. Understanding when to seek help can save you both time and resources.
Signs You Need an Expert
Not all repairs are suitable for DIY attempts. Here are some signs that necessitate contacting a professional:
- Your cooler is experiencing significant temperature fluctuations despite attempts to reset or repair it.
- Unusual noises are coming from the compressor or fans, indicating possible mechanical issues.
- There is substantial refrigerant leakage, which can be hazardous and requires specialized tools for repair.
Choosing the Right Repair Service
If you decide to hire a professional, selecting a reputable service is crucial. Consider the following when making your choice:
- Experience and specialization: Look for a service that specializes in soda coolers and has significant experience.
- Customer reviews: Research customer reviews and ratings to gauge previous satisfaction levels.
- Warranty on repairs: Choose a service that offers a warranty on labor and parts.
Evaluating Cost vs. Benefit in Repair Decisions
In some instances, a cooler may be too damaged to justify repair. Evaluating cost versus benefit is essential. Here’s how to approach this decision:
- Compare the estimated repair costs against the cost of purchasing a new unit. If repairs exceed 50% of replacement costs, consider upgrading.
- Assess the age of the cooler; if it’s old, replacement may be more economical in the long run.
- Factor in energy efficiency; modern units often have better energy ratings that can save on utility bills over time.