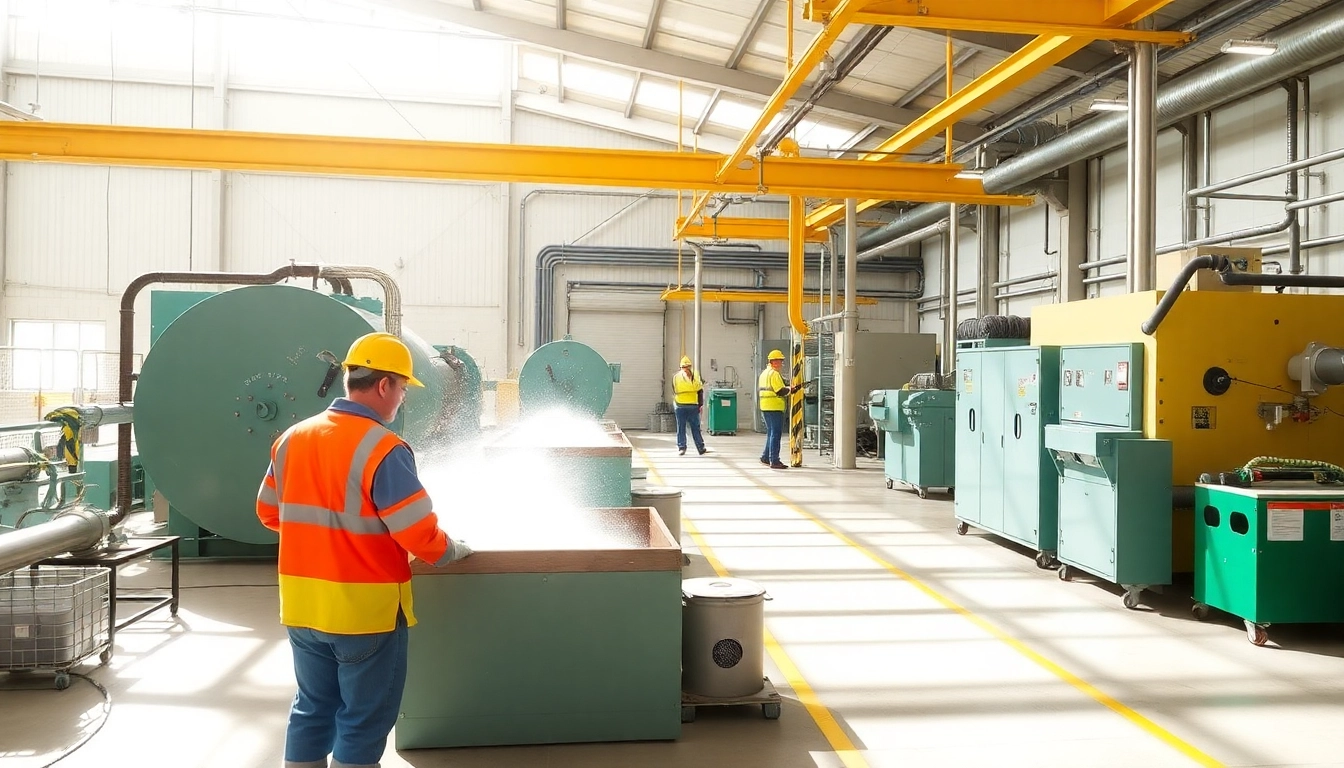
Understanding Ecoating: A Comprehensive Overview
What is Ecoating?
Ecoating, also known as electrophoretic painting or e-coating, is a sophisticated method of applying a protective, decorative coating to conductive substrates. This process involves submerging items in a solution containing paint particles, typically composed of acrylic, epoxy, or other resin-based materials. When an electric current passes through the solution, the paint particles move toward the substrate, adhering to its surface. This results in a consistent, smooth coating that cures to form a tough, durable finish.
Benefits of Ecoating in Manufacturing
Ecoating offers numerous advantages, making it an favored choice across various industries. Some key benefits include:
- Uniform Thickness: The electrostatic attraction ensures an even distribution of the coating across complex geometries, ensuring thorough coverage of the surface.
- Corrosion Resistance: E-coat finishes provide exceptional resistance to rust and corrosion, extending the lifespan of products, especially in harsh environments.
- Environmental Sustainability: Ecoating processes typically use water-based coatings, reducing volatile organic compound (VOC) emissions. This aligns with the growing emphasis on sustainable manufacturing practices.
- Cost-Effectiveness: The efficiency of the application process can lead to reduced material wastage and lower labor costs, enhancing overall profitability.
Applications of Ecoating in Different Industries
Ecoating is utilized in various sectors, including but not limited to:
- Automotive: Widely used for painting vehicle bodies, wheel rims, and undercarriage components as it provides a robust barrier against corrosion.
- Appliances: Household appliances such as refrigerators and washing machines benefit from e-coating for both aesthetic and functional protection.
- Aerospace: Components subjected to extreme conditions are often ecoated to enhance durability and performance.
- Furniture: Metal furniture is ecoated to provide a durable finish that withstands wear and tear.
Ecoating West Midlands: The Regional Advantage
Why Choose Ecoating Services in the West Midlands?
The West Midlands has emerged as a hub for ecoating services, benefiting from a combination of skilled labor, a rich manufacturing history, and a strategic location that provides access to diverse markets. Companies in this region can leverage local expertise in ecoating technologies, ensuring high-quality finishes that meet industry standards. Ecoating West Midlands reflects a concentration of providers who are not only equipped with state-of-the-art technology but also possess an understanding of customer needs, leading to bespoke solutions.
Regional Leaders in Ecoating Solutions
The West Midlands hosts several prominent ecoating providers, with facilities equipped to handle both large-scale and specialized projects. The region is home to companies like Malcolm ACP and Plastic Coatings Limited, which specialize in high-integrity finishes for automotive and industrial applications. Their commitment to quality and innovation positions them as leaders in the electrocoating field.
Local Success Stories and Case Studies
Several local manufacturers have successfully integrated ecoating into their production lines. For instance, an automotive supplier in the area implemented e-coating for its vehicle components, resulting in a 30% reduction in corrosion-related failures within the first year. This case underscores the effectiveness of e-coating in enhancing product reliability while reducing long-term maintenance costs.
The Ecoating Process: Step-by-Step
Preparation and Substrate Types for Ecoating
The ecoating process begins with thorough preparation of the substrate. The items to be coated must be cleaned and pretreated to remove all contaminants that could compromise the adhesion of the electrocoat:
- Cleaning: Surfaces undergo several cleaning stages to eliminate dirt, oil, and grease.
- Surface Preparation: Chemical treatments or abrasive blasting may be used to create a suitable surface profile.
- Rinsing: After chemical treatment, parts are rinsed to remove residues, ensuring optimal adhesion.
Substrates commonly used for ecoating include metals like steel, aluminum, and certain conductive plastics. The choice of material affects coating performance and is critical to the overall success of the finishing process.
The Electrocoating Process Explained
The electrocoating process involves multiple stages:
- Submersion: Prepared substrates are submerged in a bath of water-based paint or e-coat solution, where the paint carries a negative charge.
- Electrophoretic Deposition: An electric current is applied, attracting paint particles to the positively charged substrate. This creates a uniform and stable layer of coating on the surface.
- Curing: The coated items are removed from the bath, dried, and then cured in an oven at controlled temperatures, allowing the coating to harden and adhere properly.
This meticulous process ensures durability and reliability of the e-coat, making it suitable for various applications.
Quality Control Standards in Ecoating
To maintain high standards, ecoating facilities implement rigorous quality control measures:
- Thickness Measurement: Coating thickness is measured using non-destructive testing methods to ensure compliance with specifications.
- Visual Inspections: Finished products undergo visual checks for defects such as runs, sags, or bruises.
- Adhesion Tests: Adhesion quality is evaluated using standardized tests to ensure coatings can withstand operational stresses.
Such stringent measures help manufacturers guarantee the performance and longevity of their coated products, fostering trust with clients.
Choosing the Right Ecoating Partner
Key Factors to Evaluate in Ecoating Services
Selecting a reliable partner for ecoating requires careful assessment of several factors:
- Experience: Look for providers with a proven track record in specific industries relevant to your needs.
- Technology and Equipment: Evaluate the capability of their e-coating facilities, including the latest technologies that enhance efficiency and quality.
- Customer Support: A responsive customer service team can significantly impact your experience and satisfaction with the service.
- Customization Options: Ability to tailor coating solutions to meet specific requirements is a strong advantage.
Common Questions About Ecoating Services
Prospective customers often have queries about ecoating services, including:
- How long does the ecoating process take? Process time can vary based on the size and complexity of parts; however, most processes can be completed within a day when considering preparation and curing.
- What industries benefit the most from ecoating? Any industry utilizing ferrous or non-ferrous metals can benefit, but automotive and appliance manufacturing see particularly significant advantages.
- Is ecoating environmentally friendly? Yes, due to its use of water-based coatings and minimal waste generation, ecoating aligns well with modern sustainability goals.
How to Obtain Quotes and Estimates
Obtaining a quote for ecoating services is generally straightforward:
- Prepare specifications: Provide detailed information regarding the type, quantity, dimensions, and materials of the items requiring coating.
- Contact multiple providers: Reach out to various ecoating companies in your area to request quotes and assess their responses.
- Compare offers: Analyze the received quotations not only based on price but also service offerings, delivery timelines, and terms of service.
Future Trends in Ecoating Technologies
Innovations in Ecoating Processes
The ecoating industry is continually evolving. Innovations such as advancements in automated application processes, smart coatings with embedded sensors, and enhanced curing techniques are shaping the future of electrocoating. These developments improve efficiency, reduce costs, and enhance coating performance.
Sustainability Practices in Ecoating West Midlands
Sustainability has become a prominent concern for manufacturers. Ecoating services in the West Midlands are increasingly adopting practices such as:
- Recycling Water: Closed-loop systems are implemented in many plants to reduce water consumption and waste.
- Low-VOC Coatings: Many providers are shifting to low-VOC formulas to minimize air pollution and comply with environmental regulations.
- Energy Efficiency: Upgrading to energy-efficient curing ovens reduces energy consumption significantly, contributing to lower operational costs and carbon footprints.
The Impact of Technology on Ecoating Services
Technology is essential to optimizing ecoating processes. Innovations in spray equipment and robotic systems allow for greater precision and consistency. Additionally, software-driven monitoring systems enable real-time tracking of operations, fostering data-driven decisions for quality control and efficiency improvements.