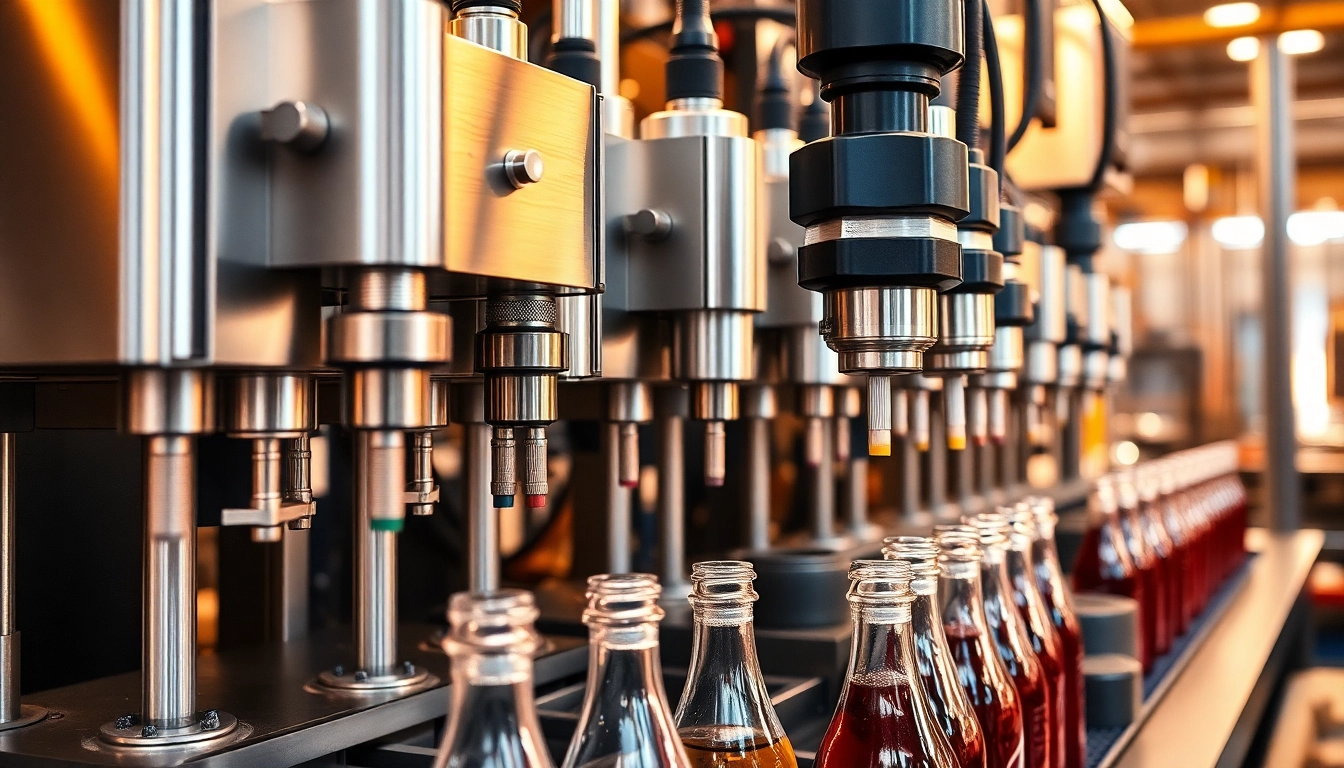
Understanding Filling Machines
What Are Filling Machines?
Filling machines are sophisticated devices designed to dispense products into various containers such as bottles, jars, pouches, and other packaging formats. They play a crucial role in numerous industries, ensuring that products are filled accurately and efficiently while maintaining the desired quality and safety standards. Filling machines can handle various types of products, including liquids, powders, granules, and pastes, depending on their design and specifications. These machines are integral to the packaging process, streamlining operations, reducing labor costs, and enhancing productivity across various manufacturing sectors.
Types of Filling Machines in the Industry
The filling machine industry encompasses a wide variety of machine types, each tailored to meet specific product requirements and production needs. Here are some common types of filling machines:
- Volumetric Filling Machines: These machines measure and dispense a specific volume of product into containers. Common applications include filling liquids, granules, and powders.
- Piston Filling Machines: Ideal for viscous liquids and pastes, these machines use a piston mechanism to dispense the product accurately.
- Weight Fillers: These machines fill containers based on weight, ensuring that each package meets the specified weight criteria.
- Gravity Filling Machines: Utilizing gravity to fill containers, this type is best suited for thin liquids and is widely used in the beverage industry.
- Aseptic Filling Machines: Designed to fill products into sterile containers in a sterile environment, these machines are essential for the pharmaceutical and food industries.
- Inline Filling Machines: Common in high-speed production settings, these machines allow continuous filling processes, increasing efficiency and productivity.
Applications Across Various Sectors
Filling machines serve multiple sectors, each with unique requirements and challenges:
- Food and Beverage: Filling machines in this sector handle juices, sauces, dairy products, and dry goods, ensuring hygiene and compliance with regulatory standards.
- Pharmaceuticals: These machines are vital for accurately dispensing medicines and supplements, where precision and cleanliness are paramount.
- Cosmetics: Filling machines for cosmetics manage various viscosities in lotions, creams, and serums, reflecting emerging trends in packaging aesthetics.
- Household Products: Cleaning agents and personal care products rely on efficient filling processes to meet consumer demand.
Choosing the Right Filling Machine Manufacturer
Key Factors in Selecting a Manufacturer
When it comes to selecting a filling machine manufacturer, several critical factors must be considered to ensure that the chosen company aligns with your specific production needs and standards:
- Experience and Expertise: Look for manufacturers with a proven track record in producing high-quality filling machines. Their expertise in the industry can be invaluable.
- Range of Products: Evaluate whether the manufacturer offers a broad range of filling machines that can accommodate various products and production capacities.
- Customization Options: The ability to customize machines based on specific needs is essential, especially for unique or specialized products.
- Customer Support: Assess the level of support provided post-purchase, including maintenance, spare parts availability, and technical assistance.
- Compliance with Industry Standards: Ensure that the manufacturer adheres to relevant safety and quality standards, particularly for sectors such as pharmaceuticals and food.
Evaluating Manufacturer Capabilities and Services
Once potential manufacturers have been shortlisted, it is crucial to evaluate their capabilities further:
- Factory Visits: Whenever possible, visit the manufacturer’s facility to observe their production processes and quality control measures firsthand.
- Client Testimonials and Case Studies: Reviews from past clients can provide insights into the manufacturer’s reliability and the performance of their machines.
- Technical Capabilities: Investigate the technological sophistication of the machines being offered. Are they equipped with advanced features like automation, user interfaces, and data analytics?
- Warranty and Service Agreements: Enquire about the warranty period and service contracts offered, as these can mitigate risks associated with equipment failures.
Benefits of Working with Established Brands
Partnering with well-known and reputable filling machine manufacturers can provide several significant advantages:
- Reliability: Established brands typically have a reputation to protect, leading to consistent quality and reliability in their products.
- Innovation: Recognized manufacturers are often at the forefront of industry innovations, incorporating the latest technologies into their machines.
- Resource Availability: Larger companies tend to have the resources to innovate and provide comprehensive customer support and service.
- Partnership Opportunities: Collaborating with established brands can open doors to additional services, such as training and technical support.
Industry Trends and Innovations
Recent Advances in Filling Technology
The filling machine industry is continuously evolving, driven by technological advances and market demands. Some notable recent trends include:
- Smart Technology: The incorporation of smart technology and IoT capabilities in filling machines allows for real-time monitoring and data collection, leading to improved efficiency and predictive maintenance.
- Flexible Equipment: As consumer preferences shift, manufacturers are investing in flexible filling machines that can quickly adapt to different product types and packaging formats.
- Robotics and Automation: Increased automation in filling processes is enhancing production speed and accuracy, reducing the need for manual labor.
- Energy Efficiency: New designs are focusing on energy saving, leading to reduced operational costs and environmental footprints.
Sustainability Practices in Manufacturing
With growing concerns about environmental impacts, many filling machine manufacturers are adopting sustainable practices:
- Eco-Friendly Materials: Manufacturers are increasingly using sustainable materials and manufacturing methods, allowing for reduced waste and a smaller carbon footprint.
- Design Optimization: Innovations focus on creating machines that use less energy, reducing the overall environmental impact.
- Recycling Initiatives: Some companies are initiating programs to recycle packaging materials, further contributing to sustainability efforts.
Automation in Filling Processes
Automation continues to be a key driver in the efficiency of filling operations. The rise of automated filling machines has significantly changed production lines:
- Increased Throughput: Automated systems enable faster filling speeds, thereby increasing overall production volume.
- Consistency and Accuracy: Automated filling processes minimize human error, ensuring that each product is filled to precisely the same volume or weight.
- Labor Cost Reduction: As automation takes over repetitive tasks, businesses can reduce labor costs and reallocating human resources to more strategic activities.
Case Studies of Successful Implementations
How Leading Brands Utilize Filling Machines
The success of filling machines can be best demonstrated through case studies from industry leaders:
For example, Accutek Packaging Equipment has helped numerous companies optimize their packaging lines by implementing advanced filling systems that cater to a variety of product types. Their ability to customize solutions has led to increased efficiencies in production. Another illustrative example is Cozzoli Machine Company, which provides specialized filling machines for the pharmaceutical industry, showcasing the adaptability of these machines to meet stringent regulatory requirements.
Lessons Learned from Top Manufacturers
There are critical lessons to be gleaned from how leading brands deploy their filling machinery:
- Adaptability: Successful manufacturers understand that flexibility in their machinery can lead to better response times to market changes.
- Continuous Improvement: Regular assessments of machinery performance help in identifying bottlenecks and areas for enhancement.
- Training and Development: Ensuring that staff are well-trained in operating advanced machinery is crucial for maintaining efficiency.
Impact on Production Efficiency
By implementing cutting-edge filling machines, companies have reported significant improvements in production efficiency. Metrics indicate:
- Reduction in product waste by up to 30% due to precise filling capabilities.
- Increased line speeds by 50% when switching to automation.
- Improvement in overall operational efficiency leading to a 20% increase in output without major capital investment.
Future Outlook for Filling Machine Manufacturers
Predicted Industry Growth and Trends
The future of filling machine manufacturers appears promising, with anticipated growth driven by several trends:
- Enhanced Customization: As demand for unique and personalized products rises, manufacturers will focus on offering machines that can efficiently handle small production runs.
- Integration of AI and Data Analytics: Future machines will increasingly utilize artificial intelligence and data analytics for better performance monitoring and predictive maintenance.
- Global Market Expansion: Emerging markets are expected to provide new opportunities for filling machine manufacturers as local industries grow.
Emerging Technologies on the Horizon
Looking ahead, several emerging technologies are likely to impact the filling machine sector:
- Blockchain for Traceability: The implementation of blockchain technology may enhance traceability in the supply chain, ensuring product integrity.
- Advanced Robotics: Robotics will play a more significant role in automation, enabling smarter filling processes and reducing downtime.
- AI-Powered Analytics: The use of AI-driven analytics can optimize filling processes by learning from historical production data and operational parameters.
Preparing for Future Challenges and Opportunities
As the industry evolves, manufacturers must be prepared to face various challenges:
- Regulatory Compliance: Staying ahead of regulatory changes will be essential for manufacturers, particularly in sensitive industries like food and pharmaceuticals.
- Supply Chain Disruptions: Developing resilient supply chains will help manufacturers mitigate the impact of external fluctuations.
- Sustainability Pressures: There will be increasing pressure to adopt environmentally friendly practices, requiring manufacturers to innovate continually.